Thinking Outside the Box
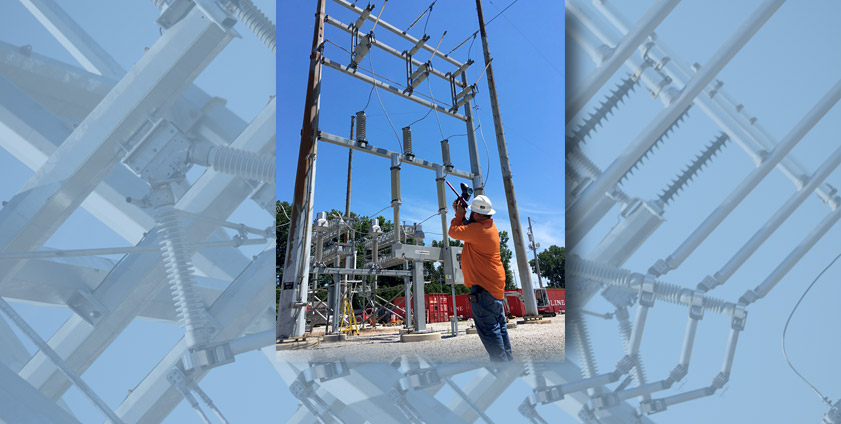
Substation Electrician Leader Andy Sebok uses a paintball gun to lubricate switches inside a CEI substation. Before using the guns, employees are required to take a training class about their safe operation.
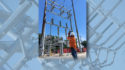
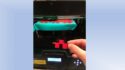
July 27, 2018
When Regional Operations Supervisor Jon Schussler was asked about using paintball guns to pre-treat equipment in substations, he says it was a game changer. “It’s one of the best preventive maintenance tools we have developed to keep our substation switches lubricated and in service.”
One of the challenges substation electricians face is attempting to operate a switch that is frozen in either the open or closed position. Trying to manipulate the switch manually can result in a sprain or strain injury, making it a safety concern for employees. A frozen switch also can create an operational issue, requiring a service interruption to make repairs.
Enter the paintball gun. Employees from The Illuminating Company (CEI) came up with the innovative idea while investigating ways to make substation switches easier and safer to operate. Electricians at CEI have been using the paintball guns for more than a year with great success.
“By lubricating the linkage points, jaws and blade ends the day before we plan to operate a switch, they open quickly and safely more than 90 percent of the time,” adds Jon. “The paintball guns are loaded with special lubrication balls filled with oil or grease, and all of the equipment is available from local retailers.”
CEI line workers also have started using paintball guns to lubricate certain pieces of overhead equipment, and the method has been shared with other FirstEnergy Utilities (FEU) operating companies.
“We’re discovering solutions to Human Performance (HP) issues in some surprising places,” says Jay Foringer, director, Operations Support, CEI. “In addition to finding a new use for paintball guns, we’ve been using 3D printing technology to enhance HP.”
3D printers use a variety of materials – most commonly plastic or metal – to create three-dimensional objects developed through a computer-aided design (CAD) program or a 3D scanner. It was just the tool Jay needed to make improvements to HP kits used during substation construction projects to help employees perform their jobs safely and efficiently.
The kits contain a variety of colorful plastic pieces that can prevent accidental electrical shorts and flag critical equipment that must not be manipulated during work. The original HP kits were purchased from another utility company; however, when CEI relay technicians began requesting items that weren’t included, Jay used a 3D printer to make them.
“We designed the requested pieces with CAD software, and then printed them out of plastic,” explains Jay. “Unfortunately, the 3D printers we purchased were designed for light use, so it took a long time to create individual components – sometimes up to four hours per item.”
After hearing about the large 3D printers that FirstEnergy’s BETA Lab recently acquired, Jay contacted the group for assistance. “BETA Lab’s new 3D printers can create objects more quickly and cost-effectively,” he adds. “The HP kits now are being used by relay testers at all FEU operating companies, and by many of our Energizing the Future contractors.”
Jay has received a lot of positive feedback about the HP kits from employees. According to Greg Mallow, supervisor, Regional Operations, the kits have made a big difference in improving HP.
“The components in the kit serve as visual aids – and physical barriers – for our relay testers to help mitigate any inadvertent tripping or electrical contact,” says Greg. “When you are working on one section of 30 different terminal blocks, having visual aids can help you stay focused on the right area or circuit.”
Greg adds, “Employees used to have their own individual technique for tracking work, sometimes using different colors of electrical tape. The HP kits have standardized the way we perform tasks at CEI substations and helped to make our jobs safer.”
Employees always are looking for ways to improve the kits, including creating new components. One planned addition is a plastic cover for control-panel switches to prevent them from getting bumped out of position.
“When it comes to improving HP at substations, we’re not afraid to think outside the box,” says Jay. “We’ll do whatever it takes to help protect employees from injury and to get the job done safely.”