Harrison Recognized for Sustainability Success
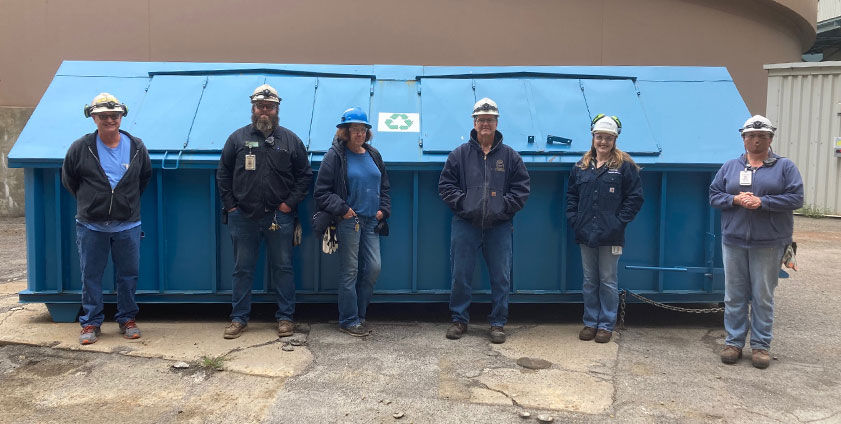
Harrison Sustainability Team members (l. to r.) Ken Yanda, Donnie Wolfe, Janet Martin, Mike Comer, Jessica Pierce and Julie Ford. Note that employees who regularly work together follow COVID-19 protocols, which depending on the situation, may not entail wearing masks. Not pictured are Gary Dinzeo (team champion and plant director), Ed Murphy (team sponsor and Technical Services manager), Adam Cetorelli, Marcy Haines, Joshua Dingess, Carla Spray, Frankie Treadway, Stewart Whitehair, Marshall Westfall and William McQuaid III.
November 23, 2020
Over successive outages, the huge booster fans that move flue gases into the Harrison Power Station emission control systems have been replaced with more efficient and robust fans. Which raises the question: what do you do with a 93,000-pound metal fan rotor when its life has ended?
Due to a special focus on sustainability at Harrison and our other generation facilities, the company is making the effort to recycle the massive equipment.
“When we started our employee-led sustainability effort a year ago, we asked for input from plant personnel, and one of the biggest items was recycling,” said Senior Scientist Julie Ford, who’s been helping coordinate the team’s activities.
However, Harrison’s program isn’t just focused on large equipment. Employees can support the effort by recycling a variety of items – from aluminum cans to cardboard.
“Members of the Sustainability Team agreed that the best way to get buy-in was to make recycling as easy as possible,” Julie said. “To do that, we implemented what’s called ‘single stream’ recycling, with employees being able to throw different kinds of waste into receptacles for separation by the recycler later.”
After some searching to locate a company willing to collect and recycle single-stream waste, Harrison’s sustainability effort was underway.
“We had our own dumpsters made and positioned them in strategic places inside and outside the plant,” Julie said. “The idea was to put them at points that were convenient for use and keep recycling top of mind.”
Signs were made, employee presentations developed. Workers learned what could, and what should not, be place in the containers. Aluminum and other metal cans, cardboard, food and beverage cartons, and most plastic containers were all able to be comingled. “I’m proud to say that our recycler has told us they’re very pleased at how clean our recycle stream is,” Julie said.
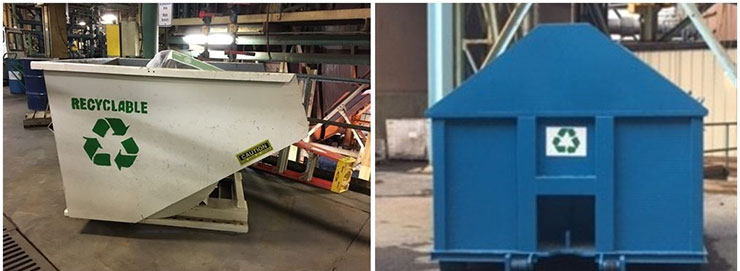
Clearly marked recycling bins are located at strategic locations inside and outside of the plant.
But the team didn’t stop there. Members started looking at what other kinds of waste might be recycled. They turned to FirstEnergy’s experts on waste and recycling streams for help.
“We look for as many opportunities as we can to recycle throughout FirstEnergy,” said Che Brindle, an advanced scientist in Coal Combustion Residuals and Waste. “We have to factor in cost and make sure that it’s affordable, and that has traditionally presented a challenge with our generation plants which, like Harrison, are not always located near the metropolitan areas where it’s easier to find recyclers.”
But seeing the Harrison team’s commitment, Che connected Julie with companies willing to accept and recycle used batteries and electronics, including old computers. “The one company refurbishes computers and gives them to low-income schools,” Che explained. “They recycle other components to fund their program. It’s a real win-win for all.”
The Harrison sustainability program also targets major construction waste, which is separated into ferrous and non-ferrous metals and set aside for recycling.
Along the way, there were some significant challenges. “COVID-19 impacted our program,” Julie noted. “Our recycler shut down for a while. But we were fortunate to find another recycler to use temporarily.”
In seven months, the Harrison program recycled nearly 10,500 pounds of mixed waste alone. The program also recycled 4,760 pounds of lead acid batteries and 5,670 pounds of electronics.
“Ultimately, our goal is to involve everyone in the plant in such a way that recycling and sustainability become second nature,” says Julie.
Recently, the Harrison Sustainability team was recognized by Fleet Operations senior staff for its commitment and results.
“We can find the outlets and talk about recycling all we want, but unless there’s buy-in at a facility it won’t be successful,” said Che. “In this case, the Harrison team came to us already excited about a program it was developing. Members want to do it, and they work hard at it. Their results prove it.”