Fort Martin Stacks Capped
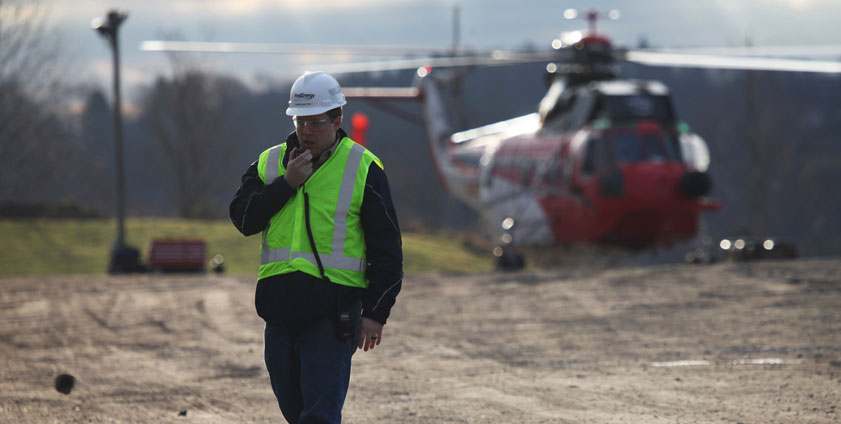
Sawyer Whitten communicates with his team during capping operations.
January 11, 2019
Just days before Christmas, workers at Fort Martin made sure nothing could come down their chimneys.
In a carefully planned, well executed procedure, two decommissioned stacks were permanently capped with enormous three-and-a-quarter ton stainless steel domes, flown into place by helicopter.
The chimneys have been out of use since 2009, when new stacks and a flue-gas desulfurization environmental system went into service. The old Units 1 and 2 stacks, located centrally in the plant, could not be torn down and so were decommissioned in place.
“When the older stacks were in operation, the high temperatures kept flue gas from condensing and attacking structural elements of the steel liner, as well as driving off moisture from the weather,” said Fort Martin Engineer Sawyer Whitten, who oversaw the installation. Unused stacks have no such protection against weather or plumes from the new stacks nearby. Resulting deterioration eventually can mean falling debris or even stack destabilization. The caps are specifically designed to prevent moisture building up and degrading the structures.
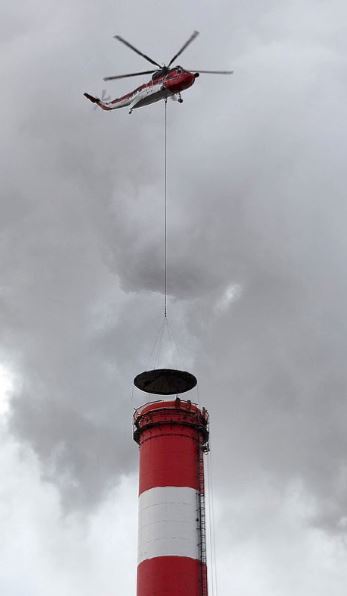
With precision, a 6268-pound steel cap is lowered to workers, who secured it to a decommissioned stack.
The caps were assembled in the lay-down yard on the hilltop above the plant. Each umbrella-shaped dome roof measures 25 feet in diameter and weighs 6268 pounds.
But because of the location and 550-foot height of the stacks, using a crane was out of the question.
The answer was a Sikorsky S61N, one of the most versatile heavy-lift helicopters.
“The contractor we hired works all over North America, in some of the most difficult circumstances,” Sawyer said. “The pilots are capable of extreme precision, and can work within tight tolerances.”
Detailed flight and job-specific safety plans were drawn up, establishing a designated 250-foot-wide flight path cleared of people and equipment. Plant access roads were controlled during lift operation, and no coal barges unloaded during the lift.
Fog delayed the helicopter arrival on the intended day of the lift. When the fog lifted, wind caused plumes from the new stack to obscure the decommissioned stack tops, a condition that caused safety concerns for the crews that would be on the stack tops to secure the caps. A detailed safety brief was conducted with crew members, but work was postponed that day.
Early in the morning the next day a second safety brief was conducted. With weather cooperating, the helicopter took off, hovering over the first cap while the group crew secured lift chains. Looking like a captured flying saucer, the heavy steel cap raised into the sky and was flown slowly and steadily to its destination high atop the former Unit 2 stack to be guided and secured by crew members. Then the chopper retrieved the second cap, and flew to the crew waiting at the top of the second stack. The entire process took less than an hour.
“Safety was our overriding consideration,” Sawyer said. “Every step of this job was meticulously planned. We were prepared to stop at any time should anyone have a concern. The completed task will make our plant a safer place for all of our employees.”
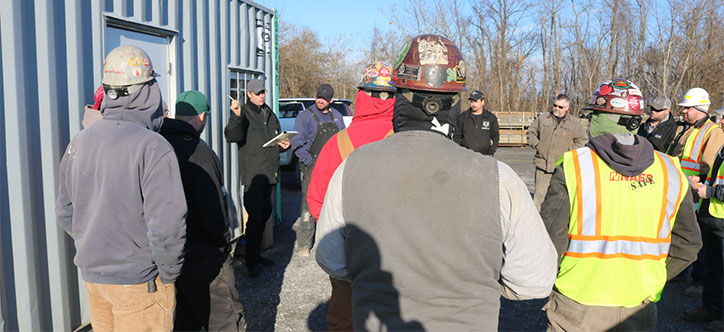
The project team listens to the helicopter pilot describe his mission during an in-depth pre-job safety brief.